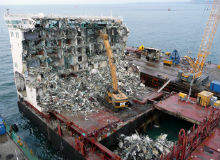
Steve Andrew is decommissioning manager and Jonathan Turner is senior project manager, at ABB Limited. For more than three decades, ABB has managed onshore decommissioning projects for the oil and gas industry.
Julian Turner: Please summarise the key findings of the recent study into decommissioning costs on the UK Continental Shelf (UKCS) undertaken by ABB Consulting.
Steve Andrew: The study has shown a belief amongst many about the financial viability of alternative removal technologies for decommissioning projects; however, others still need to be convinced and one of the aims of the report was to look at uncertainties around their adoption, and suggest ways to overcome them.
We ran two workshops and it quickly became evident that there was a lack of understanding about the potential benefits that onshore demolition and resale contractors can bring to the offshore sector.
There has been limited involvement from traditional onshore contractors due to the uncertainty of cessation of production (CoP) dates – deadlines have tended to move back. In part, this is due to the industry and the UK Government’s understandable desire to maximise revenue from the remaining reserves in the UK North Sea, with the focus on extending the life of assets.
As a result, interest from onshore demolition contractors has been effectively on hold, but there are now signs that a number of projects are moving towards decommissioning. This appears to have reinvigorated the market, with a number of non-traditional offshore contractors showing an interest in supporting the decommissioning process.
Jonathan Turner: Based on experience and reinforced through the discussions in the two industry workshops, ABB believes that there are potentially other removal opportunities than the single-lift removal concept.
How well do you really know your competitors?
Access the most comprehensive Company Profiles on the market, powered by GlobalData. Save hours of research. Gain competitive edge.
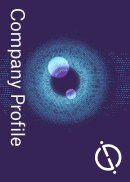
Thank you!
Your download email will arrive shortly
Not ready to buy yet? Download a free sample
We are confident about the unique quality of our Company Profiles. However, we want you to make the most beneficial decision for your business, so we offer a free sample that you can download by submitting the below form
By GlobalDataVery few companies have undertaken projects using the ‘piece small’ or ‘piece large’ methodologies, and there are few examples of these methods being used.
These methods basically cut and remove smaller platform "sections" that are then shipped to shore by a standard vessel or barge, and then reused, recycled or disposed of. By offering alternative methods, more onshore disposal yards are available to accept and process these materials and sections, generating more competition that should help to drive costs down.
Why is the cost of decommissioning in the UK North Sea set to soar to more than £40bn by 2023?
JT: When I first got involved in the industry in 2008, forecasting decommissioning on the UKCS was difficult due to a lack of information on some assets, with little benchmarking data available. Around 50% of the cost of decommissioning is spent subsea on well plugging and abandonment (P&A).
As more information becomes available these costs have been revised year-on-year using data from actual decommissioning projects and the current trend suggests the figure will continue to rise.
A large proportion of the cost is mobilisation of the decommissioning vessels. However, until recently there seems to have been a reluctance to look at multi-operator well campaigns, whereby different operators with wells scheduled for P&A in the same areas share a support vessel for P&A. This approach would potentially offer significant savings due to the reduction in mobilisation costs.
There are enough heavy and single-lift vessels currently operating in the UK North Sea to cope with current demand, but not when the peak decommissioning activity forecast for 2018-19 is reached. Operators may have to "mothball" platforms for a number of years until a vessel becomes available or be forced into an alternative removal strategy. Additional maintenance costs – suggested to be several million pounds a year – will be required to maintain a platform during this ‘lighthouse phase’.
Another opportunity for increased cost-efficiency is greater alignment between operators’ late-life and decommissioning teams. In some instances, a lack of communication between the two teams has proven costly. The decommissioning team has required equipment that has been taken out of service, and not maintained during late life, resulting in costly refurbishment works to reinstall.
At what stage in the production process should operators start planning for decommissioning?
SA: The obvious answer is in the design phase, before you even construct the installation – however it’s too late for the platforms that are currently in production. At the design stage there are more opportunities to reduce the cost of decommissioning and to develop opportunities to implement the principles of the "circular economy", and the re-use of plant and equipment.
The study highlighted a number of opportunities during this stage that would greatly increase reuse; for example, the standardisation of plant and equipment across the industry.
JT: To maximise the benefits, planning for decommissioning should start at least 3-5 years prior to CoP. This creates a greater opportunity to reduce costs – for example, by early engagement with the resale market – allows for decontamination/preservation systems to be developed, and helps to maximise the value of redundant plant and equipment, whilst preventing the unnecessary cost of preserving equipment that is not required.
By identifying what support systems are required (accommodation, support systems, cranes and so on) suitable low cost maintenance programmes can be developed to ensure they are available when required.
How can personnel safety and environmental risks be mitigated during decom projects?
SA: I remember being involved in the removal of an 11-mile subsea pipe in Australia, which had been there for nearly 50 years, and by the time the operator had got around to thinking about removing it, it was 2m under the sea floor in some places and constituted a potential environmental hazard.
One of the areas we looked at was transfer of personnel offshore using the support vessel rather than by helicopter, which is considered one of the most hazardous forms of travel.
Then there’s the additional concern of staff operating offshore. Onshore demolition contractors have significant experience removing hazardous onshore assets, working in a very safety-driven process area, with the added risks associated with working in a live process environment. Many of the onshore hazards are applicable to offshore decommissioning. The demolition industry onshore has changed over the past 30 years, driven by changes to legislation and the development of new technologies and methods.
Part of the problem – and there are current parallels with the nuclear industry here – is changing from an operating mindset that prioritises protecting asset value to a strategy that deals efficiently with redundant equipment that needs to be segregated into different recyclable materials.
For example, you might take the manhole doors off a vessel and send personnel with breathing apparatus through confined-space entries to remove solid waste materials. However, if you are not so concerned with protecting asset value, you can remove the vessel with the material inside, send it back to shore where the vessel can be cut in half, lift the top section off and dig it out with a machine, thus removing the cost of cleaning offshore and removing people from confined spaces.
How have decommissioning projects in the UK North Sea been affected by the low oil price?
JT: One of the dangers is that operators move to CoP sooner, but if there’s a lack of money available they may abandon a platform for a number of years. A refinery degrading onshore is one thing – if a platform is allowed to deteriorate offshore, you’re faced with potential safety and environmental risks plus significant maintenance and removal costs that are going to keep rising, this could result in serious structural integrity issues and further legacy issues later.
Is there a need for more collaboration between offshore operators to reduce decommissioning costs?
SA: A big push by the industry is on collaboration, sharing lessons learnt, best practice and looking at projects that could have impact on improving future decommissioning operations. This will require a culture change and a change of mindset from one of production to one of decommissioning.
There’s also much to be learnt from decommissioning projects worldwide. A lot of the offshore infrastructure in the Gulf of Mexico (GOM) has been left in place, whereas in the UK we are working to the Convention for the Protection of the Marine Environment of the North-East Atlantic (OSPAR).
This requires that any offshore infrastructure that was installed in the UK North Sea – bar items such as jackets over 10,000t and gravity based structures – must be removed. That’s not bound by cost or the potential environmental impact, so there is the potential to challenge some OSPAR regulations. While we do that we can assess the consequences of leaving that equipment in place or removing it.
In summary the report highlighted a number of potential opportunities to make saving during the decommissioning process; it’s a good start, but there is still work to do.