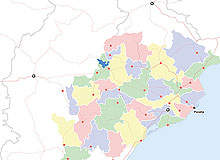
Indian Oil Corporation (IOC) built a refinery in Paradip in the Indian state of Odisha. Spread over 3,344 acres, the state-of-the-art refinery was constructed at a cost of approximately $508m. The refinery processes 15mtpa of high-sulphur heavy crude oil under nil-residue production.
The refinery was proposed in 1995 and approved by the government in 1998. The foundation stone was laid in January 2000. The project suffered several delays due to the withdrawal of tax incentives and a slump in the oil market. Final approval for the refinery was given by the IOC board in February 2009.
The project was originally expected to be completed by March 2012 and become fully operational by November 2012, but completion has been delayed due to financial constraints and the refinery was finally inaugurated in February 2016.
The new refinery produces 5.97 million tonnes of diesel, 3.4 million tonnes of petrol, 1.45 million tonnes of kerosene / jet fuel, 536,000t of LPG, 124,000t of naphtha and 335,000t of sulphur. All the products are being sold in the domestic market. The refinery is also expected to produce 200,000t of propylene, which is being exported. It helps the IOC to move into overseas markets and assists in processing low-quality crude oil.
Infrastructure
The Paradip refinery has a 300,000bpd crude and vacuum distillation unit, a 104,000bpd vacuum gas oil hydrotreater, an 80,000bpd delayed coker unit, a 78,000bpd fluidised catalytic cracker (FCC), and a 53,000bpd crude catalytic reformer.
The refinery also features a 24,000bpd paraxylene production unit, a 10,000bpd alkalination unit, a naphtha hydrotreater, a propylene recovery unit and other secondary processing facilities.
Paradip refinery facilities
In November 2009, US-based company Praxair was awarded a contract to supply hydrogen and nitrogen gases to the refinery. Praxair India signed an agreement with Uhde India in December 2009 to construct the hydrogen plant.
Praxair operates the hydrogen plant, which has a capacity of 90 million standard cubic feet a day. Construction of the plant, which uses Uhde’s steam-reformer technology, began in March 2010.
The hydrogen produced by the plant is utilised for the processing of crude oil and production of low sulphur and clean fuels. Praxair also supplies hydrogen from the plant to nearby refineries. The company also constructed a 500t a day nitrogen plant at the refinery.
Processing
The fluidised catalytic cracker uses the Indmax process developed by IOC. The process converts heavy distillate and residue into LPG and light distillate products.
The Indmax technology is a single step catalytic process and uses a proprietary catalyst. It is similar to the FCC process, but produces higher yields of LPG and light olefin.
Contractors for the Paradip refinery
In January 2007, Foster Wheeler was awarded a contract for carrying out front-end engineering design (FEED) services for the project. Foster Wheeler was appointed project management consultant and the engineering, procurement and construction management (EPCM) contractor in March 2009. The scope of the contract includes the EPCM of 15 units of the refinery including crude distillation units, reforming units, an alkalination unit, off-sites, utilities and other infrastructure.
Toyo Engineering was appointed as the offshore consultant for the FCC and propylene recovery unit of the refinery in June 2009. It provided project management, detailed engineering, construction and commissioning services for the two units.
In July 2009, Jacobs Engineering Group was appointed as the project management consultant for the delayed coker unit. Jacobs provided FEED services and also supervised the work carried out by the lump sum turnkey contractors of the unit.
Larsen & Toubro (L&T) was awarded an Rs14bn contract in March 2010 for the FCC reactor regenerator project at the refinery. L&T’s Hydrocarbon Mid and Downstream Business Group executed the project and provided engineering, construction and commissioning services.
In November 2010, Essar Projects was awarded the EPCM contract for the core processing units of the refinery, including atmospheric vacuum, naphtha hydrotreating unit and fractionator, sour water stripper and other units.
Punj Lloyd was contracted to carry out mechanical and piping works at the refinery.
KazStroyService constructed off-sites and utilities at the refinery and also carried out road works.
Dredging, Environmental & Marine Engineering reclaimed 600ha of land in Paradip for the project. Since the site of the refinery is a low-lying area, it had to be dredged to carry out construction of the refinery. This reclamation work was carried out between September 2000 and December 2001.