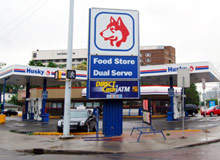
Husky Lima Refinery is a world-scale refinery in Ohio, US. Established in 1886, the refinery has changed ownership several times without ceasing operations. It is currently owned and operated by Husky Energy, which acquired the refinery from Valero Energy Corporation in 2007.
The refinery accounts for a quarter of the total gasoline consumption in Ohio. Designed to operate 24 hours a day, it produces nearly two billion gallons of refined petroleum every year. It shuts only for maintenance every five years. Plans are being made to increase the refinery’s capacity through an expansion project.
On 24 November 2009 a fire broke out in the refinery, damaging the isocracker. Repairs are being made.
Facilities
The refinery is composed of a crude unit, a stabiliser, a vacuum tower, a delayed coker, a jet bender, a naphtha hydrotreater and a splitter.
It is also equipped with an isocracker, a catalytic reformer, a diesel hydrotreater, a hydrocracker, a fluid catalytic cracker unit, a gasoline desulphurisation unit, sulphur recovery units and an aromatics unit.
Output
The refinery processes gasoline, diesel, jet fuel, residual fuels and petrochemical feedstock. It processes nearly 165,000 barrels (6,900,000 gallons) of crude oil per day. Conversion of crude oil into useful products at the refinery is performed with 94% energy efficiency.
Connection
Primary products including gasoline and diesel are transported via a pipeline. Other products are transported by truck or rail.
Refining process
The refining process at Husky Lima begins from the crude unit at the south end. Crude oil is first desalted to eradicate impurities.
It is then heated to nearly 700°F to separate it into boiling components of different ranges in atmospheric and vacuum distillation towers. From the crude unit, light material is delivered to the saturated gas plant, where light material is hydrotreated and separated into propane, butane, naphtha and refinery fuel gas.
Light naphtha passes through a C5 / C6 isomerisation unit, where the level of octane is increased. Heavy naphtha is directed to a cyclic catalytic reformer, where it is converted into a blend component with high octane. Hydrogen is produced as a co-product.
To produce benzene of chemical grade, aromatics recovery from light reformate is carried out in the aromatics unit. Before clay treatment, jet fuel from the crude unit is treated in a jet bender, which removes mercaptans.
Diesel from the crude and cracking units travels to the diesel hydrotreater, which operates at a pressure of 1,250psi. The diesel hydrotreater produces ultra-low sulphur diesel with a maximum of eight parts per million of sulphur.
The isocracker, equipped with a two-stage design reactor, takes the heavy atmospheric gas oil and cracked diesel stocks. Operating at a pressure of 1,800psi, the isocracker produces naphtha and kerosene.
North side facility
Heavy oil from the vacuum tower is sent to the north side of the refinery. In the fluid catalytic cracker (FCC), heavy oil is broken into naphtha and diesel. Light-end products produced in the FCC are sent to the unsaturated gas plant for purification. Decanted oil, also produced in the FCC, is sold in the number six heavy fuel oil market.
Hydrotreatment of FCC naphtha is carried out in the gasoline desulphurisation unit (GDU). The unit removes sulphur to less than 30 parts per million through the prime-G 2 reactor process, which also minimises octane loss.
In a two-drum coker operation, vacuum tower bottoms are thermally cracked in the coker unit. The unit makes light ends, naphtha, diesel and nearly 600t of petroleum coke per day.
The sulphur recovery unit converts acid gas released from the hydrotreaters into elemental sulphur in Claus reactors. Water is treated in the boiler house, which removes hardness and supplies high-pressure steam for the refinery.