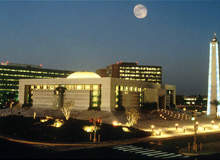
Saudi Aramco’s Abqaiq Plants facility is the company’s biggest oil processing and crude stabilisation facility. With a capacity of 7 million barrels per day, the facility is the primary oil processing site for Arabian extra light and Arabian light crude oils.
The Abqaiq Plants facility handles crude pumped from the Ghawar field. It is linked to the Shaybah oil field through a 395-mile pipeline and to the export terminal in Yanbu through a natural gas liquid pipeline.
In July 2009, Aramco partnered with Integration Objects, an industrial network security and integration provider, to optimise the plant operations and update the plant with the latest technological advancements in the industry.
Plant details
The Abqaiq Plants facility comprises three primary processing units – an oil processing unit, an NGL facility and a utilities unit. The oil processing unit consists of multiple spheroids and 18 stabiliser columns where hydrogen sulphide and light hydrocarbons are removed from the crude oil.
The NGL facility contains eight compression trains, stripper columns and de-ethaniser column. The utilities unit supplies power, steam, treated water and instrument air to the oil and NGL facilities.
The power needed by the facility is generated by six power generators comprising of three steam turbines and three combustion gas turbine generators. Steam generated by 14 boilers is supplied to the oil processing unit, NGL facility, turbines and compressors.
The water treatment plant at the facility comprises 16 reverse osmosis units, which provide demineralised water. The water produced by the plant is supplied as makeup to the boilers and heat recovery steam generators to produce the necessary steam.
The water produced by the plant is also used as drinking water for plant personnel and is supplied to the neighbouring Abqaiq community.
The Abqaiq Plants facility is equipped with two steam-driven and three motor-driven air compressors, which provide the requisite instrument air. The instrument air is used to operate control valves at the facility.
Processing
Crude oil extracted from oil wells is under pressure and contains oil, dissolved gas, salty water and small quantities of hydrogen sulphide. The oil is depressurised and separated from dissolved gases in the Gas Oil Separation Plant (GOSP).
In the GOSP, the oil is depressurised in multiple spheroids to free the dissolved gases.
After depressurisation, water and dissolved gases are extracted from the oil. The depressurised oil is sent to the stabilisation unit, where it is pumped into 18 stabiliser columns. Final gas separation and removal of hydrogen sulphide take place in the stabilisation unit.
The resultant dry, hydrogen sulphide-free, stabilised oil is sent to the refining plants in Ras Tanura and Jubail on the east coast, Yanbu on the west coast and Bapco in Bahrain.
The off-gases from the oil processing unit are sent to the NGL facility for processing.
Feed gas received from the oil processing unit is compressed in NGL’s compression trains and passed through the stripper columns and de-ethaniser column. The resultant effluent from the columns consists of overhead light gases and NGL product (oil).
The light gases are transported to other gas plants for processing and the NGL product is sent to the Ras Tanura refinery for fractionation (a separation process).
Technology
The Abqaiq Plants facility has stringent and complicated systems to ensure a continuous flow of process data. The facility has a Unix and VMS-based system architecture that runs the plant’s operations.
The architecture comprises 23 point-to-point connections connected to the distributed control systems and other automation islands with the plant information management system.
Each connection catered to a particular need of the plant. However, over time the system architecture expanded and became more complex.
The complex nature of the system and phase-out of VMS from the market made it difficult to update and maintain the system. It also increased the operational budget of the plant.
Aramco selected Integrated Objects to simplify and upgrade the system architecture, and enable it to adapt to future changes in the plant control systems. Integrated Objects decided to use industrial standard solutions and shift the plant from Unix and VMS operating system to a Windows operating system.
OLE for Process Control (OPC) was chosen as the solution to simplify the system architecture.