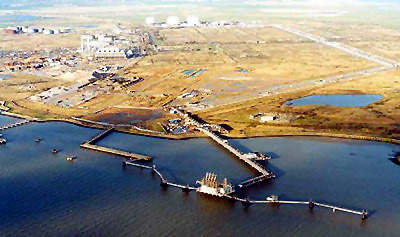
The Grain LNG Terminal is situated on the Isle of Grain on the River Medway, Kent, 30km east of London. The facility began life in 1982 as an LNG peak shave storage facility, and was used to support the gas supply grid at times of high demand.
In 2002 the owner of the facility, National Grid, began work to convert the storage facility into an LNG importation terminal. This conversion was completed and commissioned in July 2005 when the facility became operational. With North Sea gas is in decline importation terminals are becoming more important.
The LNG terminal has the capacity to receive and process up to 3.3 million tonnes of LNG (4.4 billion cubic metres of gas) a year, equivalent to 13 million cubic metres (140GWh) of gas a day.
A 20-year contract with BP / Sonatrach allows the National Grid to import LNG into the UK from other countries.
Gas demand is expected to increase by at least 15% over the next ten years and dependence on imports is expected to approach 50% by 2010. The Grain LNG site is one of four strategically located LNG terminals being developed in the UK.
Grain LNG phase I
Delivered LNG at the site is pumped through cryogenic pipelines into four 50,000m³ storage tanks (9% nickel-steel, double-containment tanks insulated with Purlite) ready to be passed to the NTS following regasification.
Skanska led the £130m phase I project, which involved the construction of a 1km-long jetty and a 4.5km cryogenic pipeline system, which was rated at 12,000m³ per hour (5,000t per hour). The contract involved new compressors, vaporisers and connections to the four refurbished storage tanks to achieve more efficient and large-scale boil-off gas compression for ship offloading at the site.
Electrical and instrumentation installation and testing on the main regasification plant associated with the LNG importation terminal was provided by Balfour Kilpatrick. Advantica provided safety, process and commercial support to the conversion project.
Grain LNG terminal construction
Work to triple the terminal capacity to 9.9 million tonnes per year completed in 2008 (comprising 12% of UK gas demand). Work on phase II started in early 2005 and was completed in December 2008. This involved the construction of three new state-of-the-art LNG storage tanks (190,000m³ – 50m high with a 92.4m diameter), each holding as much as the existing plant.
Investment for the phase II expansion is £350m. The capacity was sold to three customers: Sonatrach (Algeria), Centrica and Gaz de France, and became available by the fourth quarter of 2008.
A further expansion (phase III) at Grain LNG was announced in May 2007. It is expected to provide an additional five million tonnes of capacity in time for the fourth quarter of 2010. Construction work will include a second jetty and an additional total containment LNG storage tank of 190,000m³. Plans for the fourth phase of expansion are also under consideration at the National Grid.
Isle of Grain site
The site at Grain is ideally suited since the National Grid had existing LNG storage facilities and owns a significant area of further land around it for construction.
The River Medway and the associated sea approach are deep enough for the largest LNG ships, carrying up to 205,000m³ of LNG to the berth. The site also has an existing connection to the high-pressure National Transmission System (NTS) and is close to the main centre of demand in the UK.
The 20-year contract specifies 140GWh of capacity but can go up to 186GWh if required (the National Grid never owns the gas but just charges for regasifying). Grain LNG’s workforce has increased with phase II coming onstream.
Grain LNG contractors
For phase II, EPC (engineer, procure, construct) contractor Chicago Bridge and Iron’s (CB&I) remit was to increase the gasification and send out capacity and the boil-off gas handling capacity.
The contract also included the installation of a new control and administration facility and related systems. Control and automation systems are based on Honeywell’s Experion system.
LNG terminal operation
LNG is shipped to the terminal from various countries including Trinidad, Algeria, Egypt and Qatar. The majority of the 60 shipments to the terminal so far have been via Membrane tankers, which feature giant double-wall metal containers and typically transport about 125,000m³ of liquefied gas.
The carriers dock at the jetty unloading station, which has three 16in loading arms and a 16in vapour return arm. These feed the gas into a pipeline system comprising a single 36in line with a 14in LNG recirculation line.
The 4.5km recirculation pipelines include expansion loops that allow movement as the pipe cools down. The recirculation pipe system sits above ground on concrete sleepers. As well as transferring the LNG, the cryogenic pipelines are designed to manage flash gas surge and heat ingress issues during the initial stages of the offloading procedure.
The main line consists of 400 welded pipe sections with only two bolted flanges to optimise its integrity. The pre-insulated pipes of a nickel-steel construction insulated with flexible PUR foam insulation are designed to transmit the forces induced by the thermal contraction of the steel pipe to the HDPE casing. The pipelines are also run full and cold to prevent thermal cycling of the pipeline.
Grain LNG employs four 38-bar compressors for unloading the ship and two two-bar units for day-to-day operations when not unloading.
The compressors operate at suction temperatures down to -160°C; the gas exiting at -135°C is then passed through a superheater to reduce its temperature to around 5°C.
The submerged combustion vaporisers feature a combustion burner in a water bath to vaporise LNG as it passes through a stainless steel ladder, tubular heat exchanger. Gas outlet temperature is around 5°C and achieves outputs of 17t per hour to 170t per hour.
The composition of some of the LNG imports does not meet UK natural gas specifications and so requires nitrogen ballasting. The Air Products nitrogen plant generates around 300t of gaseous nitrogen a day and is backed up with a 1,000t liquid nitrogen storage facility.