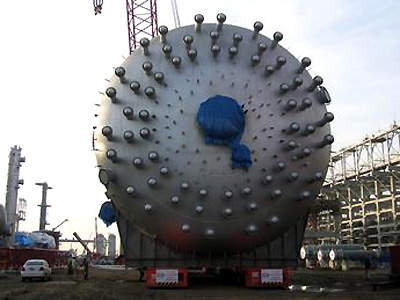
The Sohar Refinery Company was set up in 2003 to construct, commission and operate a new grass roots refinery in Wilayat of Sohar, Oman (250km northwest of the capital Muscat). The company is 20% owned by the Oman Oil Company and 80% by the government of Oman.
Oman has only one refinery in Muscat and it was felt that such an oil-rich country should have a greater degree of independence in the refinery sector, hence the facility. The Sohar refinery was designed to process a mixed feedstock of Oman crude oil and atmospheric residue from the Oman Refining Company.
In 2010, the Sohar Refinery Company planned a $300m expansion to increase the output capacity of feedstock, refined products and other petroleum by-products. The expansion will increase the refinery’s capacity from 116,000bpd to 187,000bpd and expected to be completed by 2013.
Sohar Refinery facilities
The refinery has an atmospheric distillation crude unit with a capacity of 116,400bpd and a residue fluidised catalytic cracking (RFCC) unit with a capacity of 75,260bpd. The refinery also has an LPG Merox unit, a petrol desulphurisation unit, a 1,900,000Nm³/d hydrogen generation unit, sour water stripping unit, amine regeneration unit (ARU), sulphur recovery unit, indirect alkylation (InAlK) unit and a deep desulphurisation unit. and a deep desulphurisation unit.
The refinery operates for maximum olefin production to supply 340,000t per year of propylene to Oman Polypropylene plant. Around 10% of the refined products are sold in local markets with the remainder made available for export.
The refinery output for export includes fuel oils, petrol, LPG, naphtha, gas oil and kerosene. The exports will be through a ten-year off-take agreement with BP.
The refinery is also used to treat (desulphurisation) fuel oils produced at Mina Al-Fahal, crude oil exporting terminal in Muscat. A 266km pipeline has also been built to transport fuel and crude oil from the Mina Al-Fahal facility to the refinery, which cost an estimated $175m.
A major maintenance shutdown was planned at the refinery in order to optimise the refining process and enhance the plant’s reliability.
The refinery was closed for approximately two months from January to February 2010 for implementing the projects for the planned improvements. The projects include repairing / replacing the corroded pipelines, heat exchanger and installation of a catalyst. The work tenders for the same were issued in August 2009.
Refinery finance
The Sohar refinery cost $1.3bn, which was 90% financed by debt through a series of loans from a number of financial institutions, including Japanese Bank for International Cooperation (direct loan of $261.9m), Nippon Exports Insurance Company ($261.9m), Bank of Tokyo Mitsubishi and a further ten banks ($907.8m).
Bank of America Securities was appointed as the financial advisor to the project and the Omani Government stake in the project is overseen by the Oman Ministry of Finance.
Contractors and construction
The engineering procurement and construction (EPC) contract for the project was awarded to a Japanese consortium (JGC Corporation and Chiyoda) in July 2003 for a lump sum of $880m. The project documents were signed in December 2003. JGC Corporation had already carried out the front-end engineering and design (FEED) contract for the refinery in 2000 and was responsible for the design and commissioning of the facility.
ABB Lummus were the project managers and LG Caltex the maintenance and operations contractor. SK Engineering of South Korea was also involved in the management and operation of the refinery.
Consolidated Contractors was appointed subcontractor for all process and utilities work and provided three cranes for the lifting of heavy sections during construction. The three cranes were a 1,600t PTC containerised platform twin-ring lattice boom, a 1,000t Demag C4800 (both hired from Mammoet) and a 400t Demag CC2400.
Other cranes on site provided by Consolidated Contractors include a 200t American 225, a 165t American 9299, a 125t American 9260 and a 100t Grove GMK 5100.
TransTel Engineering was awarded the telecommunications contract for the new refinery in March 2004. This was a turnkey package involving the design, engineering and commissioning of an integrated telecommunications system within the refinery to include video, radio, voice and data systems.
Construction of the refinery was started in the first quarter of 2004 and the project was structurally completed by April 2006.
In February 2011, CB&I Lummus was awarded a $40m FEED and project management services contract for the refinery expansion project. Scope of work for CB&I includes debottlenecking and increasing capacities of the existing units and installing of clean fuels units. Others bidders for the project included Larsen & Toubro.
Refinery technology
The technology chosen for the new refinery for etherification included a system from Fortums (NExTAME), which was installed by Neste Engineering. This system is used to produce ethers; the NExTAME unit produces the preferred high-oxygen petrol component, which is a mixture of tertiary amyl methyl ether and other heavier ethers used for oxygenate blending (although some ethers, such as tertiary butylmethyl ether, are being phased out due to their poisonous effect on water supplies if accidentally spilled).
In addition, the French company ISP was chosen to provide its PRIME-G+ desulphurisation technology.
Pipeline
The oil transportation pipeline (24in) from Mina Al-Fahal to Sohar can transport 116,000bpd of feedstock (mixed crude and long residue), and will later be modified to accommodate 160,000bpd.
The conceptual study for the pipeline was carried out by Mott McDonald in October 2003. The FEED contract was awarded to ILF and Partner and the project management consultants were Mott McDonald.
The contract for the pipeline construction was awarded to Saipem / CCC joint venture. The pipeline was completed in time for the refinery’s commissioning in 2006.
Integrated petrochemical facilities
A number of other production plants were constructed at the site to take advantage of feedstocks from the refinery. The Oman Polypropylene Plant (OPP) a joint venture of Oman Oil Company, LG Engineering and ABB Lummus cost $200m and was constructed in parallel with the refinery at Sohar. It can produce 327,000t/y of propylene.
In addition, a polyethylene plant was constructed adjacent to the new refinery in Sohar by Dow Chemical (50%) in a joint venture with the Oman Oil Company (25%) and the Oman government (25%).
Desulphurisation project
The Sohar Refinery project involved the installation of an 18,000bpd unit to reduce sulphur levels in fuel oils to 50ppm. The recovered sulphur would be marketed for sulphuric acid production. The project was managed from the start by a team from ORC, the diesel hydro desulphurisation unit was licensed by Haldor Topsoe of Denmark and the sulphur unit by Jacobs Engineering, Netherlands.
The FEED was carried out by Granherne and the project construction contract was awarded to SK Construction and Engineering of South Korea for a sum of $32.2m. The construction subcontractor was Bahwan Engineering. The project was completed in mid-2006.
Supply contract
In January 2011, Oman Methanol signed an agreement with Sohar Refinery to supply methanol from its 3,000t complex. Both the plants will be connected by a proposed pipeline. The agreement will stop Sohar Refinery’s dependence on methanol imports.
Problems at the refinery
In October 2007, it was reported that Oman Refining Company had merged with the Sohar Refinery Company to form a single company called Oman Refineries and Petrochemicals Company (ORPC). The Sohar Refinery also suffered from a number of pre-commissioning problems which have prevented it from working at full capacity.
The plant has had problems with its pipework due to corrosion because the contractor used the wrong alloy in the pipes and it was unable to stand up to normal operations (first discovered in October 2006).
Work on repairing / replacing large sections of the refinery pipe work was completed in February 2009. It was reported that the plant ran at 50%–70% of capacity until the remedial work was completed.
There was also a design fault with the residual fluid catalytic cracker (no bypass between the crude distillation unit and the secondary units), which had to be rectified.
The problems with the refinery meant that the polypropylene plant situated next to the refinery was short of the propylene feedstock it needed to operate and had to source supplies elsewhere at increased cost. The cost overrun on the refinery project stood at $200m.