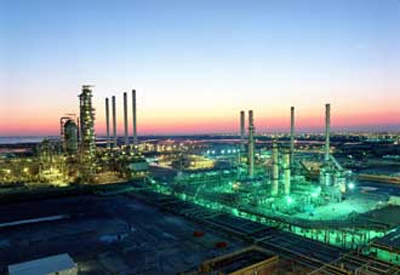
Saudi Aramco began construction on two major projects: the Khursaniyah oil and gas programme and the Hawiyah Natural Gas Liquids (NGL) recovery programme in September 2005.
The Khursaniyah oil and gas programme will develop oil and gas production facilities for the onshore Abu Hadriya, Fadhili and Khursaniyah oil fields near Jubail Industrial City in the Eastern Province, with daily capacity reaching 500,000 barrels of crude oil by December 2007.
The Hawiyah NGL recovery programme will produce an additional 310,000 barrels of ethane and NGL products a day through the Hawiyah NGL Plant near the Ghawar Field and the Ju’aymah Gas Fractionation Plant near Ras Tanura (this is also undergoing expansion); this project will be ready for production in early 2008.
The NGL plant will process an additional one billion standard cubic feet a day of natural gas and 80,000bpd of hydrocarbon condensate. In addition, the programme will install central utilities, including two cogeneration units each with a capacity of 150MW as well as water treatment and steam generation facilities to serve Khursaniyah Producing Facilities (KPF) and Khursaniyah Gas Plant (KGP). KPF and KGP are the heart of the Khursaniyah programme.
CONTRACTS
The company awarded five contracts, valued at SR4.5bn ($1.2bn), to build one of the world’s largest NGL plants at Hawiyah to recover ethane and NGL from around four billion standard cubic feet a day (scf/d) of sales gas.
These projects are part of the Aramco plan to boost crude oil production capacity by 2.3 million barrels a day by 2009, bringing it to roughly 12.5 million barrels a day, in order to keep a cushion of 1.5 million to two million barrels a day capacity. These projects will increase the amount of lighter-end crude oil and products Aramco produces, helping it capture more of the refinery market in Asia and the US, which prefer lighter oils to the often heavy sour crudes typical of Saudi exports.
The additional ethane and natural gas liquids stripped out of rising gas production may be spiked into the Saudi crude oil stream or sold directly to refiners who use them to make cleaner burning gasoline.
KHURSANIYAH OIL AND GAS PROGRAMME
Snamprogetti of Italy was selected for the Front Engineering and Design (FEED) project of the Khursaniyah production facilities and was also chosen to execute the construction.
The scope of work includes building a central Gas-Oil Separation Plant (GOSP) and wet crude handling facilities to process crude from the three fields (140 oil and water wells), gas gathering compression facilities, a cogeneration plant, crude stabilisation and water injection. The project will treat 500,000bpd of crude oil and 450,000bpd of injection water.
A consortium of Bechtel Overseas of London and Technip of Rome was selected for the FEED project of the Khursaniyah Gas Plant and also to execute construction.
The work includes the construction of two trains of gas conditioning and ethane and NGL recovery with a total capacity of one billion standard cubic feet a day of sour gas. The facilities will also produce 560 million standard cubic feet a day of sales gas and 300,000bpd of ethane and NGL and 1,800t of sulphur.
The construction work has involved the building of 500km of gas, oil and water pipeline, 250km of flowlines, 300km of 13.8kV power line, cathodic protection systems, and new communications systems for voice and data.
In addition to this has been the design and construction of the facilities themselves on the 49km² site, which has been fast tracked cutting 12 months off the building process schedule.
The gas project is expected to be completed by the end of November 2007.
HAWIYAH NGL RECOVERY PROGRAMME
JGC Corporation of Japan was awarded the FEED and execution contract for the Hawiyah NGL and related infrastructure, this will consist of three NGL recovery trains, product surge and shipping facilities, other service utilities, tank and process control system. Snamprogetti will undertake the work related to gas treating and compression facilities, which will include inlet distribution, two gas treatment trains, sales gas compression, and electrical system and support facilities.
Contracts for the communication, plant infrastructure facilities and temporary camp and catering services for the construction workers were signed with local contractors: General Telecom & Engineering (GTE), Modern Arab Construction (MAC) and National Engineering Services and Marketing Agency (NESMA).
Tecnicas Reunidas of Spain was awarded an EPC contract for a further expansion of the Ju’aymah gas fractionation plant as part of the same Hawiyah NGL recovery programme. This contract requires the construction of a fourth train to fractionate 270,000bpd of ethane and NGL and 100,000bpd of propane and NGL for the refining and petrochemicals market.
GAS PLANT AT HAWIYAH
Aramco is following a plan which has been in action since the early 2000s to expand non-associated gas reserves and the related gas processing and distribution network known as the master gas system. It is hoped that this will help satisfy the growing domestic and industrial demands for gas as fuel and feedstock.
The overall plan is the gas expansion programme. Hawiyah gas plant was part of this original plan and was brought on-stream in December 2001. The facility can process up to 1.6 billion standard cubic feet a day of raw gas (sweet and sour) and produce 1.4 billion standard cubic feet a day of sales gas for the master gas system, 170,000bpd of condensate, and 1,000tpd of sulphur.
Facilities at the plant, in addition to the four gas-processing trains that perform gas dehydration, dew-point control and sales-gas compression, include two gas sweetening and sulphur recovery trains, two condensate stabilisers and two sour-water strippers. The expansion programme currently underway will significantly increase these production figures and improve the economic viability of the plant.