
Offshore rig decommissioning in the North Sea in recent years has resulted in a new service sector being generated in the oil and gas industry. And with future decommissioning projects valued at £23bn in UK waters alone, it looks set to thrive.
While this youthful industry has opened up many doors for companies to expand their service offering, timescales, limited technology and ever-changing legislations are still holding it back.
North West Hutton platform
Weighing around 20,000t and consisting of 21 modules and seven caissons, the North West Hutton platform is the only fixed steel jacket installation of its size currently being decommissioned in the North Sea.
Installed in 1981 and located 130km north-east of the Shetland Islands, the removal of the North West Hutton platform is one of the North Sea’s most ground-breaking and expensive decommissioning projects yet.
After undergoing two decades of oil and gas recovery, the platform ceased production in July 2002, recouping only 126 million barrels of oil equivalent (boe) of the field’s estimated 487-million-barrel reserves. In 2006, Heerema Marine Contractors was awarded a contract for the removal and onshore disposal and recycling of the platform.
How well do you really know your competitors?
Access the most comprehensive Company Profiles on the market, powered by GlobalData. Save hours of research. Gain competitive edge.
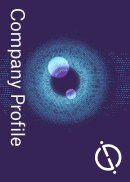
Thank you!
Your download email will arrive shortly
Not ready to buy yet? Download a free sample
We are confident about the unique quality of our Company Profiles. However, we want you to make the most beneficial decision for your business, so we offer a free sample that you can download by submitting the below form
By GlobalDataMeeting new demands – the growth of a market
Because of the platform’s size, the North West Hutton operators had stringent requirements for the method of removal, and, as a result, innovative cutting technology was developed specifically for the project. Commissioned by Heerema Marine Contractors, Cutting Underwater Technologies (CUT UK) provided its leading cutting services for the partial removal of the North West Hutton platform.
Although CUT already had diamond wire technology in place before the project, the sheer size of the North West Hutton platform resulted in the development of new machines and methodologies to suit the client’s needs, according to Duncan Griffiths, sales and marketing manager of CUT UK.
“The big things introduced onto North West Hutton were an actual machine and a methodology,” Griffiths says. “The machine was what we call a modular unit, which basically meant that we could take out the centre section so that one machine could cut a much higher range of cutting diameters.”
As a result of using the modular unit, fewer tools, less deck space and fewer people were required, which ultimately resulted in cost savings for Heerema. In addition, the company developed the castellated cut in response to Heerema’s concerns about stability in the platform’s structure.
“Normally with a diamond wire, we would cut through a structure diagonally,” Griffiths says. “The client, however, thought that if we did this on the majority of legs, it might cause instability. So they wanted to cut it but retain some stability and strength in the structure.”
As a result, the castellated cut methodology came about. “As its name suggests, it offers a castellated profile to the cut,” says Griffiths. “So the stability remains intact and it lifts the structure directly from where it is. If you forgive the pun, it really is the cutting-edge of technology in this field.”
Troubled timescales for decommissioning
The North West Hutton project may have allowed CUT to develop new technology, but Griffiths says decommissioning also poses some risks anyone entering the service industry should be wary of.
“The problem is timescales,” he says. “From the service side we are of course dependent on the outcome of the regulatory decision and that depends on the oil price and 101 other things.”
Constant changes to the predicted timings of decommissioning projects creates difficulties in planning, meaning that no company can rely on just decommissioning work to survive.
With conditions as they currently stand, Griffiths says it is impossible to survive as just a service provider in the decommissioning market. “The way we look at it, it is the icing on the cake,” he says. “We’ve seen four or five major projects in the last few years and for the next two, three years, there’s nothing.
“You’ve got to be prepared to wait because time keeps moving to the right, people change their mind. You can end up quoting the same job over several years so it can be frustrating when you’re having to develop your technology and they turn around and so, we’ll do it next year or the year after.”
According to Oil & Gas UK operations and supply chain director Paul Dymond, changes to forecasted timings in the decommissioning industry make it difficult for all service providers to establish an effective marketplace.
Ever-changing plans can create problems for contractors unable to make necessary arrangements or plan for a strong workforce and technical support, which can delay the development and implementation of new technology.
Griffith understands this only too well. “One of the main problems is they keep moving the goalposts,” he says. “You’re geared up to work within the existing legislation [but you may be] brought in on the removal of [a rig] 1m below the seabed and you design your machines to do that, and the next minute it’s 3m. So you change your designs again, and then its 5m. So you’re investing a lot of money in machines designed to do the job in line with legislations and then they change it.”
North Sea decommissioning summit
Despite being an industry that is full of opportunities, offshore decommissioning in the North Sea has significant obstacles to overcome.
Key players plan to address these issues at the EyeforEnergy’s 6th Annual North Sea Decommissioning Summit taking place in Aberdeen on 11-12 November 2010.
Griffiths, who chaired at last year’s decommissioning conference, explains why the summit is a crucial time for leading service providers to discuss the industry’s challenges now that projects are taking place. “We’ve had four major jackets come out in the last two years so there is a lot more on the actual experience rather than just this is what we do when we get the job done.”
As for CUT, Griffiths says that North West Hutton was the company’s best experience to date. “North West Hutton was up there with the technology and methodology – the castellated method, which is unique to us. Everything went really well and it was a project we were very pleased and proud to be involved in.”