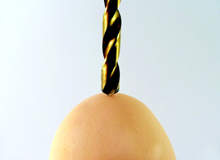
Technology development for the oil and gas sector has many potential targets among the complex processes in exploration and production, but the need to extend the value of mature assets and reach further into their reserves focuses considerable investment on drilling systems.
Mature fields can pose problems due to pressures from depleted formations, which necessitate a better understanding of subsurface structures, and in some cases the need for extra casing strings to improve well stability.
Quicker production
“Obviously the lion’s share of what we produce is from mature fields, so any incremental change on these assets can increase production more quickly. There is a lot of interest in how to develop brownfield sites further,” says Brett Borland, manager, drilling technology at ConocoPhillips.
“We are drilling longer horizontal wells past depleted zones in order to develop more of the reservoir, so we must look at geomechanics to understand how we can get through the subsurface, and we need to solve the problem of adding more casing to the wellbore. New technologies for wellbore strengthening will continue to be important,” he adds.
Years of research and investment by Tesco Corporation led to the revolutionary technique of casing drilling. Standard oilfield casing is used to drill the well and remains in place to case it.
The technology has been seen to deliver improvements in drilling speed by eliminating problems such as drill-string tripping.
By lowering and retrieving a bottom hole assembly (BHA) inside the casing it can in some cases be a safer and speedier alternative, and in the past ten years it has built a track record of success in commercial wells.
“In mature fields where we see a weakening of the subsurface due to lower reservoir pressure, casing drilling may give us the wellbore strength we need to develop brownfield sites,” says Borland.
In offshore applications directional casing while drilling (DCwD) is proving a viable and reliable tool for use in challenging wells, having been tested extensively and deployed in the North Sea by ConocoPhillips.
The dawn of DCwD
DCwD is a unique solution on wells that experience problems with lost circulation and wellbore stability. These types of problems often arise during well construction in mature fields. In most instances, casing while drilling is done using a non-retrievable bit that is attached to the bottom of the casing and remains in the hole.
DCwD with a retrievable BHA provides the flexibility to steer the wellbore while offering the potential to further improve wellbore stability and reduce the number of casing strings that are needed.
A further advantage of DCwD is that the rotation adds strength to the wall of the borehole. This is because of the “plastering effect”, which is sometimes referred to as a smear or stress cage.
The technology is a viable solution in situations where conventional drilling hits a time-consuming and costly obstruction. The collapse of a wellbore can result in a lengthy process of reconditioning the hole or having to sidetrack and drill a new hole section, but the developers of the technology – Schlumberger and Tesco Corp observe that DCwD can save rig time in such instances, as well as bringing down the cost of well construction and potentially improving well control by enabling circulation to take place when the BHA is being moved in the well.
These qualities were first put to the test in an offshore development when the technology was utilised on the Eldfisk Bravo platform in the Norwegian part of the North Sea, which is operated by ConocoPhillips. In total the application on this project saw almost 11,000ft successfully drilled and positioned correctly using retrievable BHAs.
The implementation of DCwD was a success that built faith in the technology, and its use has since been extended to other ConocoPhillips assets.
“At one field in particular casing drilling is an enabling technology that allows us to get through an intermediate section that has been very problematic in the past. Now we drill with casing and are not seeing the problems, which we had struggled with while employing conventional drilling technology. Since then CwD has become a standard technology on each new well drilled in that field,” says Borland.
The next level
Considering the benefits that DCwD can deliver, it is reasonable to ask why it has not been adopted more rapidly by the industry. One of the key factors that will determine the use of casing drilling in the near future is cost, especially as the industry is keenly pursuing optimal efficiency.
Nevertheless DCwD is a technology that will be greatly needed in applications where the challenging conditions of a well – especially in mature fields where there are depleted formations – defy conventional drilling techniques. In cases where it is an enabling technology it is by definition more cost effective than leaving a well undrilled.
“It is a tool that you need in specific applications. You want to drill the most cost-effective well that you can and if conventional drilling gets you where you need to be faster, then you are likely to stick to it. That is why casing drilling is not more widely used throughout the market at the moment,” says Borland.
“There is a lot of equipment and personnel involved, so there is a cost associated with using the technology. And often it is needed only for a small proportion of the well. We use it on hole sections where casing drilling is an enabling technology, which includes fields in Norway and Alaska, but we also want to minimise its impact on the operations, so we use DCwD where it provides benefits without fundamentally changing the way we do the work,” he adds.
The advantages of DCwD in offshore fields
- Lower well construction costs
- Reduced pipe handling improves safety for personnel
- Enhanced well control due to circulation while tripping
- Proven and tested to be a robust technology
- Fewer casing strings required
- Higher-quality, stronger wellbores
- Casing rotation while drilling adds further strength to the wellbore due to the plastering effect
- Retrievable BHA can be raised and lowered using wireline or drillpipe
- Availability of trained and experienced support teams from technology developers Schlumberger and Tesco Corporation
- Applicable for the most popular sizes of casing
- Rugged, rotary steerable system (RSS).
Since the first implementation, there has been a process of learning how to use and refine the technology, and Borland notes that future use of DCwD may be approached differently.
“When we did the first trial offshore in Norway we did a full rig modification, which included putting in a split crown derrick modifications and installing a wireline winch. Looking back, we would not make the same changes. For example, we would not look to retrieve the assembly with wireline, but on the drillpipe instead. We would want to go about it in a way that puts less pressure on the existing infrastructure,” he remarks.
The parameters governing the use of DCwD may change in the future as the process of refinement adds new capability to the technology. One of the key goals in the process will be to enable DCwD systems to cope better with more intense and challenging conditions in the well.
“A major challenge for us now is in our high pressure/high temperature projects, so we will look at the potential to use casing drilling where those HP/HT fields need wellbore strengthening,” says Borland.
Schlumberger is set to focus on further developing DCwD with its rotary steerable systems (RSS) technology. Its PowerDrive RSS range plays a significant role in optimising directional drilling, delivering less drag, higher rates of penetration, lower risk of sticking and improved hole cleaning.
Drilling speed is increased because there are no stationary parts to cause friction or anchor the BHA in the hole, and using RSS can improve the flow of cuttings past the BHA through continuous rotation and because no annular bottlenecks are created.
Future development of DCwD with RSS is likely to focus on using a smaller casing size.
Schlumberger has noted that there has been an overwhelming acceptance of DCwD with RSS in smaller hole sizes, observing that for 7in casing there has been a 500% increase in footage drilled than has been seen with larger sizes of casing.
For ConocoPhillips, DCwD technology remains invaluable in some fields, particularly where it is the only viable option for navigating challenging formations and providing the necessary wellbore stability to allow the well to be completed cost effectively. While the company continues to use casing drilling it has not yet identified any candidates for immediate use of DCwD, but it will be a powerful tool in its kit for developing fields in the future.
Specific applications
Borland recognises that the industry understands the principles that make DCwD a valuable technology, but he also understands why it has not become more prevalent. It is a tool for specific applications where conditions demand something other than conventional drilling techniques.
Nevertheless, he observes that when the technology is seen in action it arouses a great deal of interest, as it quickly proves its worth.
“Most people are not willing to use DCwD unless they have an undrillable well, but when they do use it they realise how well it works. It improves wellbore strength and allows full return and the ability to drill to the next casing point. Lost circulation or a weak bore hole can lead to a huge loss of time, so DCwD can greatly improve efficiency,” he remarks.
The industry has a valuable tool at its disposal, and over time DCwD could become important enabling technology in many more fields.
The question you have to ask is: why is casing drilling solving lost circulation problems and strengthening the wellbore? The term plastering or smear effect was adopted early on when ConocoPhillips was utilising casing drilling in the Lobo field in South Texas.
This same result has now been repeated on ConocoPhillips assets in Alaska, New Mexico and offshore Norway, whereby lost circulation and/or a significant increase in fracture gradient was achieved after a portion or all of a wellbore section was drilled with casing. These results are not always seen with just the cuttings generated by the bit, the addition of granular lost circulation material has proven to enhance the results.
DCwD at the Eldfisk Bravo field
Retrievable borehole assembly incorporated a range of sophisticated technology:
- PowerDrive X5 rotary steerable systems (RSS) that replace conventional tools such as mud motors and enable directional drilling with continuous rotation from the surface
- PowerPak straight positive displacement motors (PDMs) for steerable motor service in directional drilling that include power sections for greater torque or extra power
- Real-time PowerPulse and TeleScope systems for telemetry and surveying.
Casing strings were rotated at speeds of between 20rpm and 30rpm from the surface.
PDMs added an extra 130rpm to the RSS, polycrystalline diamond compact (PDC) bits and under-reamer.
Rate of penetration was variable, achieving 80ft/h at its peak.
All directional objectives were achieved in a complex well, in which the maximum dogleg severity reached a peak of 4.83°/100ft.